نہیں یہ بورنگ نہیں ہو گا، ایماندارانہ طور پر اگر آپ کو ربڑ کی لچکدار چیزیں پسند ہیں۔ اگر آپ پڑھتے ہیں، تو آپ کو تقریباً ہر وہ چیز مل جائے گی جو آپ کبھی بھی ایک حصے کے سلیکون سیلنٹ کے بارے میں جاننا چاہتے تھے۔
1) وہ کیا ہیں۔
2) انہیں کیسے بنایا جائے۔
3) انہیں کہاں استعمال کرنا ہے۔
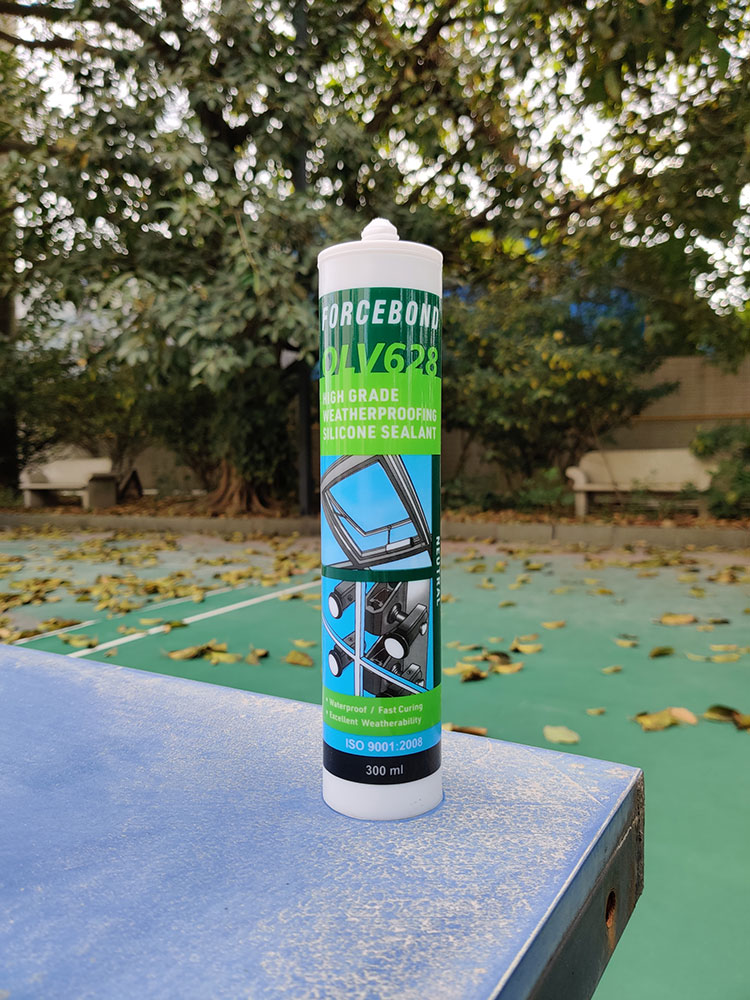
تعارف
ایک حصہ سلیکون سیلانٹ کیا ہے؟
کیمیاوی طور پر علاج کرنے والے سیلینٹس کی بہت سی قسمیں ہیں- سلیکون، پولی یوریتھین اور پولی سلفائیڈ سب سے زیادہ مشہور ہیں۔ یہ نام شامل مالیکیولز کی ریڑھ کی ہڈی سے آتا ہے۔
سلیکون ریڑھ کی ہڈی ہے:
سی – او – سی – او – سی – او – سی
ترمیم شدہ سلیکون ایک نئی ٹکنالوجی ہے (کم از کم امریکہ میں) اور درحقیقت اس کا مطلب ہے سائلین کیمسٹری سے ٹھیک ہونے والی نامیاتی ریڑھ کی ہڈی۔ ایک مثال الکوکسیلین ختم شدہ پولی پروپیلین آکسائڈ ہے۔
یہ تمام کیمسٹری یا تو ایک حصہ یا دو حصے ہو سکتے ہیں جو ظاہر ہے کہ ان حصوں کی تعداد سے متعلق ہیں جن کی آپ کو چیز کو ٹھیک کرنے کی ضرورت ہے۔ لہذا، ایک حصہ کا مطلب صرف ٹیوب، کارتوس یا بالٹی کو کھولنا ہے اور آپ کا مواد ٹھیک ہو جائے گا۔ عام طور پر، یہ ایک حصے کے نظام ہوا میں نمی کے ساتھ رد عمل ظاہر کرتے ہوئے ربڑ بن جاتے ہیں۔
لہذا، ایک حصہ والا سلیکون ایک ایسا نظام ہے جو ٹیوب میں اس وقت تک مستحکم رہتا ہے جب تک کہ ہوا کے سامنے آنے پر، یہ سلیکون ربڑ پیدا کرنے کے لیے ٹھیک نہیں ہوتا ہے۔
فوائد
ایک حصہ سلیکون کے بہت سے منفرد فوائد ہیں۔
-جب صحیح طریقے سے مرکب کیا جائے تو وہ بہترین آسنجن اور جسمانی خصوصیات کے ساتھ بہت مستحکم اور قابل اعتماد ہوتے ہیں۔ کم از کم ایک سال کی شیلف لائف (جس وقت آپ اسے استعمال کرنے سے پہلے ٹیوب میں چھوڑ سکتے ہیں) معمول کی بات ہے کچھ فارمولیشنز کئی سالوں تک چلتی ہیں۔ سلیکون میں بھی بلاشبہ بہترین طویل مدتی کارکردگی ہوتی ہے۔ ان کی جسمانی خصوصیات وقت کے ساتھ بمشکل تبدیل ہوتی ہیں جس کا UV کی نمائش سے کوئی اثر نہیں ہوتا ہے اور اس کے علاوہ، وہ بہترین درجہ حرارت کے استحکام کو ظاہر کرتے ہیں جو دوسرے سیلانٹس کے مقابلے میں کم از کم 50℃ سے زیادہ ہے۔
-ایک حصہ سلیکون نسبتاً تیزی سے ٹھیک ہو جاتا ہے، عام طور پر 5 سے 10 منٹ کے اندر جلد کی نشوونما ہوتی ہے، ایک گھنٹہ کے اندر ٹیک فری ہو جاتی ہے اور ایک دن سے بھی کم وقت میں تقریباً 1/10 انچ گہرے لچکدار ربڑ سے ٹھیک ہو جاتی ہے۔ سطح پر ایک اچھا ربڑ کا احساس ہے۔
-چونکہ انہیں پارباسی بنایا جا سکتا ہے جو اپنے آپ میں ایک اہم خصوصیت ہے (پارباسی سب سے زیادہ استعمال ہونے والا رنگ ہے)، ان کو کسی بھی رنگ میں رنگنا نسبتاً آسان ہے۔
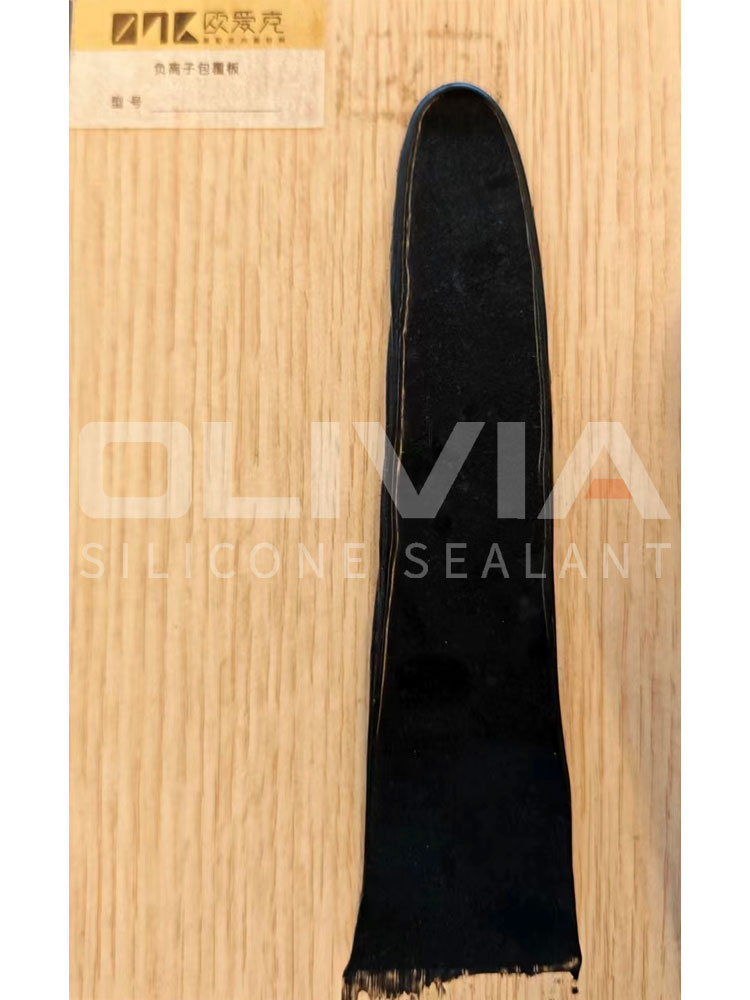
حدود
سلیکون کی دو اہم حدود ہیں۔
1) انہیں واٹر بیس پینٹ سے پینٹ نہیں کیا جا سکتا ہے- یہ سالوینٹ بیس پینٹ کے ساتھ بھی مشکل ہو سکتا ہے۔
2) ٹھیک کرنے کے بعد، سیلنٹ اپنے کچھ سلیکون پلاسٹائزر کو چھوڑ سکتا ہے جو کہ عمارت کے توسیعی جوائنٹ میں استعمال ہونے پر، جوائنٹ کے کنارے پر بدصورت داغ پیدا کر سکتا ہے۔
بلاشبہ، ایک حصہ ہونے کی نوعیت کی وجہ سے علاج کے ذریعے تیزی سے گہرا حصہ حاصل کرنا ناممکن ہے کیونکہ نظام کو ہوا کے ساتھ رد عمل کرنا پڑتا ہے اس لیے اوپر سے نیچے کی جانب علاج ہوتا ہے۔ تھوڑا سا زیادہ مخصوص ہو رہا ہے، سلیکون کو موصل شیشے کی کھڑکیوں میں واحد مہر کے طور پر استعمال نہیں کیا جا سکتا کیونکہ۔ اگرچہ وہ بڑے پیمانے پر مائع پانی کو باہر رکھنے میں بہترین ہیں، لیکن پانی کے بخارات علاج شدہ سلیکون ربڑ سے نسبتاً آسانی سے گزر جاتے ہیں جس کی وجہ سے IG یونٹس کو دھند پڑتی ہے۔
مارکیٹ کے علاقے اور استعمال
ایک حصے کے سلیکون کا استعمال تقریباً کہیں بھی اور ہر جگہ کیا جاتا ہے، بشمول، کچھ عمارت کے مالکان کی مایوسی کے لیے، جہاں مذکورہ بالا دو حدود مسائل کا باعث بنتی ہیں۔
تعمیراتی اور DIY مارکیٹوں کا بڑا حجم ہے جس کے بعد آٹوموٹو، صنعتی، الیکٹرانکس اور ایرو اسپیس ہیں۔ جیسا کہ تمام سیلینٹس کے ساتھ، ایک حصے کے سلیکونز کا بنیادی کام پانی یا ڈرافٹس کو آنے سے روکنے کے لیے دو ملتے جلتے یا مماثل ذیلی ذخیروں کے درمیان خلا کو قائم رکھنا اور پُر کرنا ہے۔ کبھی کبھی کسی فارمولیشن کو زیادہ بہاؤ کے قابل بنانے کے علاوہ شاید ہی تبدیل کیا جائے جس پر یہ ایک کوٹنگ بن جاتی ہے۔ کوٹنگ، چپکنے والی اور سیللنٹ کے درمیان فرق کرنے کا بہترین طریقہ آسان ہے۔ ایک سیلنٹ دو سطحوں کے درمیان سیل کرتا ہے جبکہ ایک کوٹنگ صرف ایک کو ڈھانپتی ہے اور اس کی حفاظت کرتی ہے جبکہ ایک چپکنے والی دو سطحوں کو بڑے پیمانے پر ایک ساتھ رکھتی ہے۔ سیلانٹ زیادہ تر چپکنے والی کی طرح ہوتا ہے جب اسے ساختی گلیزنگ یا موصل گلیزنگ میں استعمال کیا جاتا ہے، تاہم، یہ اب بھی دو ذیلی ذخیروں کو ایک ساتھ رکھنے کے علاوہ سیل کرنے کا کام کرتا ہے۔
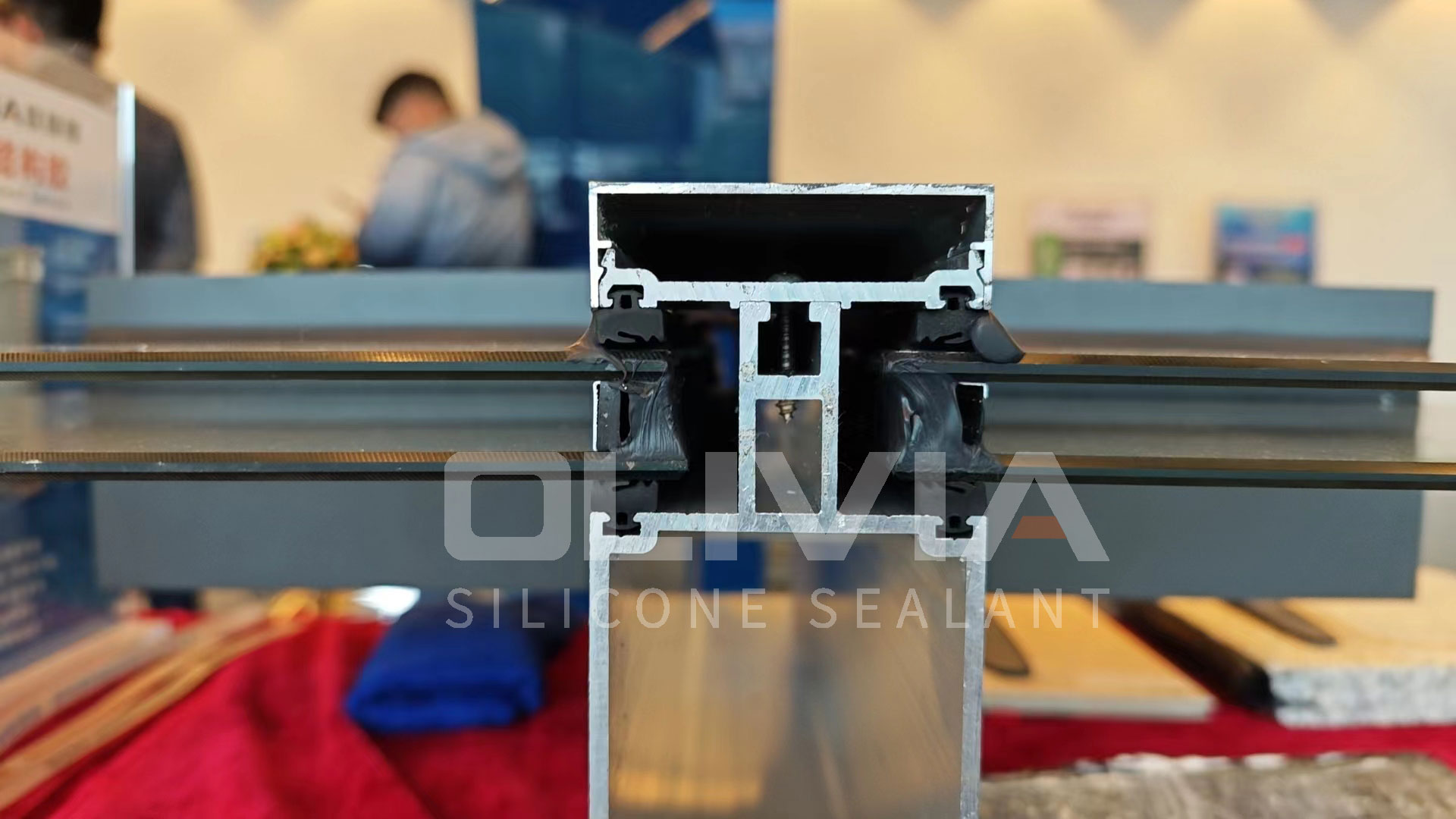
بنیادی کیمسٹری
غیر ٹھیک شدہ حالت میں سلیکون سیلنٹ عام طور پر ایک موٹے پیسٹ یا کریم کی طرح لگتا ہے۔ ہوا کے سامنے آنے پر، سلیکون پولیمر کے رد عمل والے اختتامی گروپس (پانی کے ساتھ رد عمل ظاہر کرتے ہیں) اور پھر ایک دوسرے کے ساتھ مل جاتے ہیں، پانی چھوڑتے ہیں اور لمبی پولیمر زنجیریں بناتے ہیں جو ایک دوسرے کے ساتھ رد عمل ظاہر کرتے رہتے ہیں یہاں تک کہ پیسٹ ایک متاثر کن ربڑ میں بدل جاتا ہے۔ سلیکون پولیمر کے آخر میں رد عمل کا گروپ فارمولیشن کے سب سے اہم حصے سے آتا ہے (خود پولیمر کو چھوڑ کر) یعنی کراس لنکر۔ یہ کراس لنکر ہے جو سیلنٹ کو اس کی خاص خصوصیات دیتا ہے یا تو براہ راست بدبو اور علاج کی شرح، یا بالواسطہ طور پر جیسے رنگ، چپکنے، وغیرہ، کیونکہ دیگر خام مال جو مخصوص کراس لنکر سسٹمز جیسے فلرز اور ایڈیشن پروموٹرز کے ساتھ استعمال کیے جا سکتے ہیں۔ دائیں کراس لنکر کا انتخاب سیلنٹ کی حتمی خصوصیات کا تعین کرنے کی کلید ہے۔
علاج کی اقسام
علاج کرنے کے کئی مختلف نظام ہیں۔
1) Acetoxy (تیزابی سرکہ کی بو)
2) آکسائم
3) الکوکسی
4) بینزامائیڈ
5) امین
6) امینوکسی
آکسائمز، الکوکسی اور بینزامائڈز (زیادہ وسیع پیمانے پر یورپ میں استعمال ہوتے ہیں) نام نہاد نیوٹرل یا غیر تیزابی نظام ہیں۔ امائنز اور امینوکسی سسٹم میں امونیا کی بدبو ہوتی ہے اور یہ عام طور پر آٹوموٹو اور صنعتی علاقوں یا مخصوص بیرونی تعمیراتی ایپلی کیشنز میں زیادہ استعمال ہوتے ہیں۔
خام مال
فارمولیشنز میں کئی مختلف اجزاء ہوتے ہیں، جن میں سے کچھ اختیاری ہوتے ہیں، مطلوبہ اختتامی استعمال کے لحاظ سے۔
صرف بالکل ضروری خام مال ری ایکٹو پولیمر اور کراس لنکر ہیں۔ تاہم، فلرز، آسنجن پروموٹرز، نان ری ایکٹیو (پلاسٹکائزنگ) پولیمر اور کیٹالسٹ تقریباً ہمیشہ شامل کیے جاتے ہیں۔ اس کے علاوہ، بہت سے دیگر additives استعمال کیے جا سکتے ہیں جیسے کہ کلر پیسٹ، فنگسائڈس، شعلہ retardants، اور ہیٹ سٹیبلائزر۔
بنیادی فارمولیشنز
ایک عام آکسائم کی تعمیر یا DIY سیلنٹ کی تشکیل کچھ اس طرح نظر آئے گی:
% | ||
Polydimethylsiloxane، OH نے 50,000cps کو ختم کیا۔ | 65.9 | پولیمر |
Polydimethylsiloxane، trimethylterminated، 1000cps | 20 | پلاسٹکائزر |
میتھیلٹریوکسیمینوسیلین | 5 | کراس لنکر |
امینو پروپیلٹریتھوکسیلین | 1 | آسنجن پروموٹر |
150 sq.m/g سطحی رقبہ فومڈ سلکا | 8 | بھرنے والا |
Dibutyltin dilaurate | 0.1 | اتپریرک |
کل | 100 |
فزیکل پراپرٹیز
عام جسمانی خصوصیات میں شامل ہیں:
لمبائی (%) | 550 |
تناؤ کی طاقت (MPa) | 1.9 |
100 لمبا (MPa) پر ماڈیولس | 0.4 |
ساحل ایک سختی | 22 |
وقت کے ساتھ جلد (منٹ) | 10 |
ٹیک فری ٹائم (منٹ) | 60 |
سکریچ ٹائم (منٹ) | 120 |
علاج کے ذریعے (24 گھنٹے میں ملی میٹر) | 2 |
دوسرے کراس لنکرز کا استعمال کرتے ہوئے فارمولیشن ایک جیسے نظر آئیں گے شاید کراس لنکر کی سطح، آسنجن پروموٹر کی قسم اور کیورنگ کیٹالسٹس میں مختلف ہوں۔ ان کی جسمانی خصوصیات قدرے مختلف ہوں گی جب تک کہ سلسلہ بڑھانے والے شامل نہ ہوں۔ کچھ سسٹم آسانی سے نہیں بنائے جا سکتے جب تک کہ چاک فلر کی ایک بڑی مقدار استعمال نہ کی جائے۔ اس قسم کی فارمولیشنز واضح طور پر واضح یا پارباسی قسم میں تیار نہیں کی جا سکتیں۔
سیلانٹس تیار کرنا
ایک نیا سیلانٹ تیار کرنے کے 3 مراحل ہیں۔
1) لیبارٹری میں تصور، پیداوار اور جانچ - بہت کم حجم
یہاں، لیب کیمسٹ کے پاس نئے آئیڈیاز ہیں اور وہ عام طور پر تقریباً 100 گرام سیلنٹ کے ہینڈ بیچ سے شروع کرتے ہیں صرف یہ دیکھنے کے لیے کہ یہ کیسے ٹھیک ہوتا ہے اور کس قسم کا ربڑ تیار ہوتا ہے۔ اب FlackTek Inc کی طرف سے ایک نئی مشین "The Hauschild Speed Mix" دستیاب ہے۔ یہ خصوصی مشین ہوا کو باہر نکالتے ہوئے ان چھوٹے 100g بیچوں کو سیکنڈوں میں ملانے کے لیے مثالی ہے۔ یہ اہم ہے کیونکہ اب یہ ڈویلپر کو ان چھوٹے بیچوں کی جسمانی خصوصیات کی جانچ کرنے کی اجازت دیتا ہے۔ فومڈ سلکا یا دیگر فلرز جیسے کہ تیز چاک کو تقریباً 8 سیکنڈ میں سلیکون میں ملایا جا سکتا ہے۔ ڈی ائیرنگ میں تقریباً 20-25 سیکنڈ لگتے ہیں۔ مشین ایک دوہری غیر متناسب سینٹری فیوج میکانزم کے ذریعے کام کرتی ہے جو بنیادی طور پر ذرات کو خود اپنے مکسنگ بازو کے طور پر استعمال کرتی ہے۔ زیادہ سے زیادہ مکس سائز 100 گرام ہے اور کئی مختلف قسم کے کپ دستیاب ہیں جن میں ڈسپوزایبل بھی شامل ہے، جس کا مطلب ہے بالکل کوئی صفائی نہیں۔
تشکیل کے عمل میں کلید صرف اجزاء کی قسم نہیں ہے، بلکہ اضافے اور مکس اوقات کی ترتیب بھی ہے۔ قدرتی طور پر ہوا کا اخراج یا ہٹانا مصنوعات کی شیلف لائف رکھنے کے لیے اہم ہے، کیونکہ ہوا کے بلبلوں میں نمی ہوتی ہے جس کی وجہ سے سیلنٹ اندر سے ٹھیک ہو جاتا ہے۔
ایک بار جب کیمسٹ اس قسم کی سیلنٹ حاصل کر لیتا ہے جو اس کے مخصوص استعمال کے لیے 1 کوارٹ پلینٹری مکسر تک کی ضرورت ہوتی ہے جو تقریباً 3-4 چھوٹی 110 ملی لیٹر (3oz) ٹیوبیں بنا سکتی ہے۔ یہ ابتدائی شیلف لائف ٹیسٹنگ اور آسنجن ٹیسٹ کے علاوہ کسی بھی دیگر خصوصی ضروریات کے لیے کافی مواد ہے۔
اس کے بعد وہ 1 یا 2 گیلن مشین پر جا سکتا ہے تاکہ مزید گہرائی سے جانچ اور کسٹمر کے نمونے لینے کے لیے 8-12 10 اوز ٹیوبیں تیار کرے۔ سلینٹ کو برتن سے دھاتی سلنڈر کے ذریعے کارٹریج میں نکالا جاتا ہے جو پیکیجنگ سلنڈر کے اوپر فٹ بیٹھتا ہے۔ ان ٹیسٹوں کے بعد، وہ پیمانے کے لیے تیار ہے۔
2) اسکیل اپ اور فائن ٹیوننگ میڈیم والیوم
بڑے پیمانے پر، لیب فارمولیشن اب ایک بڑی مشین پر تیار کی جاتی ہے جو عام طور پر 100-200 کلوگرام یا تقریباً ایک ڈرم میں ہوتی ہے۔ اس قدم کے دو بنیادی مقاصد ہیں۔
a) یہ دیکھنے کے لیے کہ آیا 4 lb سائز اور اس بڑے سائز کے درمیان کوئی اہم تبدیلیاں ہیں جس کا نتیجہ اختلاط اور پھیلاؤ کی شرح، رد عمل کی شرح اور مکس میں سراسر کی مختلف مقداروں سے ہو سکتا ہے، اور
ب) ممکنہ گاہکوں کے نمونے لینے کے لیے کافی مواد تیار کرنا اور کام پر کچھ حقیقی فیڈ بیک حاصل کرنا۔
یہ 50 گیلن مشین صنعتی مصنوعات کے لیے بھی بہت مفید ہے جب کم حجم یا خاص رنگوں کی ضرورت ہوتی ہے اور ایک وقت میں ہر قسم کا صرف ایک ڈرم تیار کرنا ہوتا ہے۔
مکسنگ مشینوں کی کئی اقسام ہیں۔ دو سب سے زیادہ استعمال ہونے والے سیاروں کے مکسرز (جیسا کہ اوپر دکھایا گیا ہے) اور تیز رفتار منتشر ہیں۔ ایک سیارہ اعلی viscosity کے آمیزے کے لیے اچھا ہے جبکہ ایک disperser خاص طور پر کم viscosity کے بہاؤ کے قابل نظاموں میں بہتر کارکردگی کا مظاہرہ کرتا ہے۔ عام تعمیراتی سیلانٹس میں، یا تو مشین اس وقت تک استعمال کی جا سکتی ہے جب تک کہ کوئی ایک تیز رفتار ڈسپرسر کے اختلاط کے وقت اور ممکنہ حرارت پیدا کرنے پر توجہ دیتا ہے۔
3) مکمل پیمانے پر پیداوار کی مقدار
حتمی پیداوار، جو کہ بیچ یا مسلسل ہو سکتی ہے، امید ہے کہ پیمانے کے اوپر کے مرحلے سے حتمی فارمولیشن کو آسانی سے دوبارہ تیار کیا جائے گا۔ عام طور پر، مواد کی نسبتاً کم مقدار (2 یا 3 بیچز یا 1-2 گھنٹے لگاتار) پہلے پیداواری سازوسامان میں تیار کی جاتی ہے اور معمول کی پیداوار شروع ہونے سے پہلے اس کی جانچ پڑتال کی جاتی ہے۔
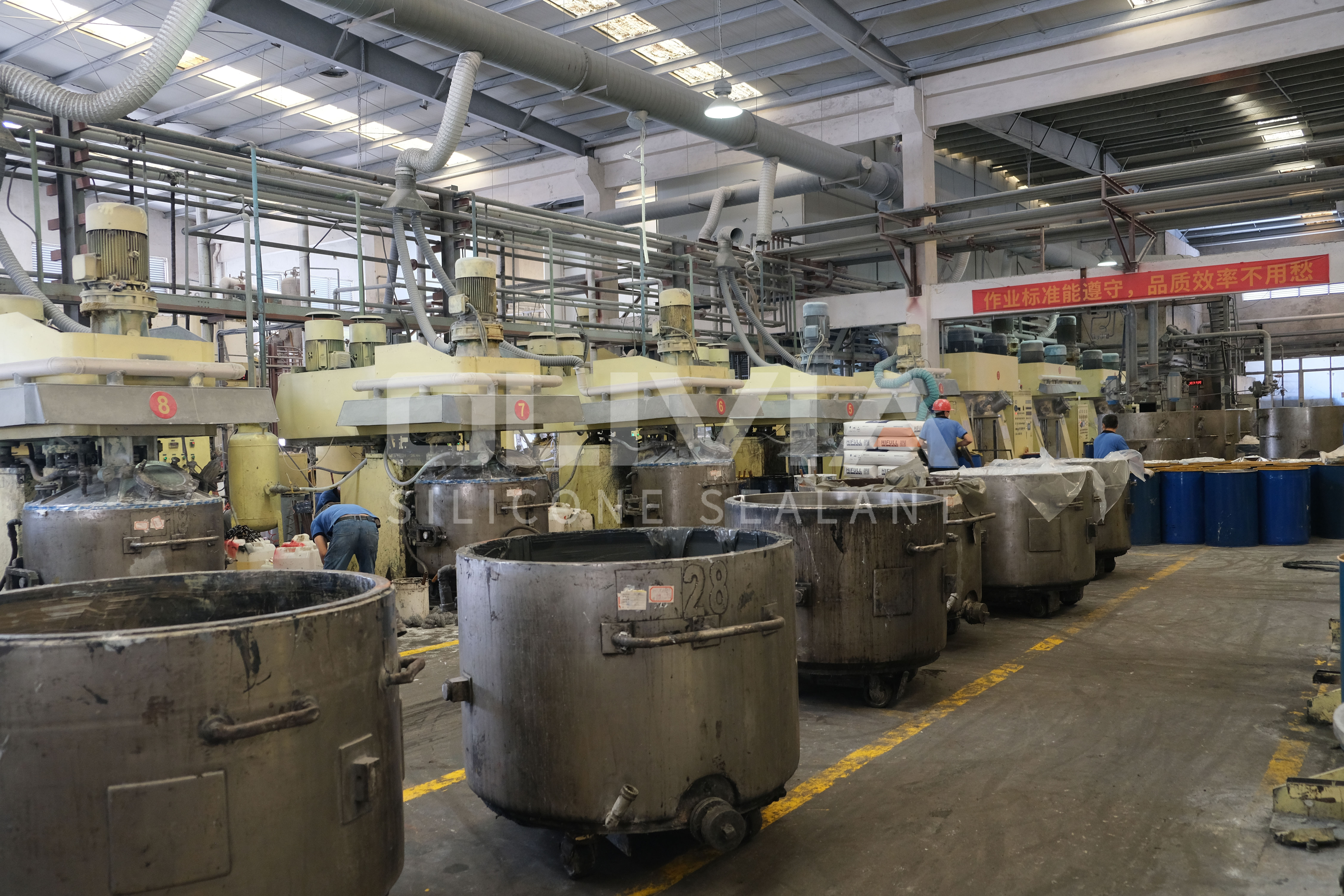
ٹیسٹنگ - کیا اور کیسے ٹیسٹ کرنا ہے۔
کیا
جسمانی خصوصیات - لمبا ہونا، تناؤ کی طاقت اور ماڈیولس
مناسب سبسٹریٹ سے چپکنا
شیلف لائف - دونوں تیز اور کمرے کے درجہ حرارت پر
علاج کی شرح - وقت کے ساتھ جلد، ٹیک مفت وقت، سکریچ ٹائم اور علاج کے ذریعے، رنگوں کے درجہ حرارت میں استحکام یا مختلف سیالوں جیسے تیل میں استحکام
اس کے علاوہ، دیگر اہم خصوصیات کی جانچ پڑتال یا مشاہدہ کیا جاتا ہے: مستقل مزاجی، کم بدبو، سنکنرنیت اور عمومی ظاہری شکل۔
کیسے
سیلانٹ کی ایک شیٹ نکالی جاتی ہے اور اسے ایک ہفتے تک ٹھیک ہونے کے لیے چھوڑ دیا جاتا ہے۔ اس کے بعد ایک خاص گونگی گھنٹی کو کاٹ کر ٹینسائل ٹیسٹر میں ڈال دیا جاتا ہے تاکہ جسمانی خصوصیات جیسے کہ لمبائی، ماڈیولس اور تناؤ کی طاقت کی پیمائش کی جا سکے۔ وہ خاص طور پر تیار کردہ نمونوں پر آسنجن/ہم آہنگی قوتوں کی پیمائش کے لیے بھی استعمال ہوتے ہیں۔ سادہ ہاں-نہیں چپکنے والے ٹیسٹ زیربحث ذیلی جگہوں پر ٹھیک شدہ مواد کی موتیوں کو کھینچ کر کیے جاتے ہیں۔
A Shore-A میٹر ربڑ کی سختی کی پیمائش کرتا ہے۔ یہ آلہ ایک وزن اور ایک گیج کی طرح لگتا ہے جس میں ایک نقطہ کو ٹھیک شدہ نمونے میں دبایا جاتا ہے۔ جتنا زیادہ نقطہ ربڑ میں داخل ہوتا ہے، ربڑ اتنا ہی نرم اور قدر کم ہوتی ہے۔ ایک عام تعمیراتی سیلنٹ 15-35 کی حد میں ہوگا۔
وقت کے ساتھ جلد، ٹیک فری ٹائم اور جلد کی دیگر خصوصی پیمائش یا تو انگلی سے کی جاتی ہے یا وزن کے ساتھ پلاسٹک کی چادروں سے۔ پلاسٹک کو صاف کرنے سے پہلے کے وقت کی پیمائش کی جاتی ہے۔
شیلف لائف کے لیے، سیلنٹ کی ٹیوبیں یا تو کمرے کے درجہ حرارت پر پرانی ہوتی ہیں (جس میں قدرتی طور پر 1 سال کی شیلف لائف ثابت ہوتی ہے) یا بلند درجہ حرارت پر، عام طور پر 50℃ کے لیے 1,3,5,7 ہفتے وغیرہ۔ عمر بڑھنے کے عمل کے بعد (تیز حالت میں ٹیوب کو ٹھنڈا ہونے کی اجازت ہوتی ہے)، مواد کو باہر نکالا جاتا ہے جہاں سے ٹیوب کو نکالا جاتا ہے۔ ان چادروں میں بننے والے ربڑ کی طبعی خصوصیات کو پہلے کی طرح جانچا جاتا ہے۔ مناسب شیلف لائف کا تعین کرنے کے لیے ان خصوصیات کا موازنہ تازہ مرکب مواد سے کیا جاتا ہے۔
مطلوبہ زیادہ تر ٹیسٹوں کی مخصوص تفصیلی وضاحت ASTM ہینڈ بک میں مل سکتی ہے۔
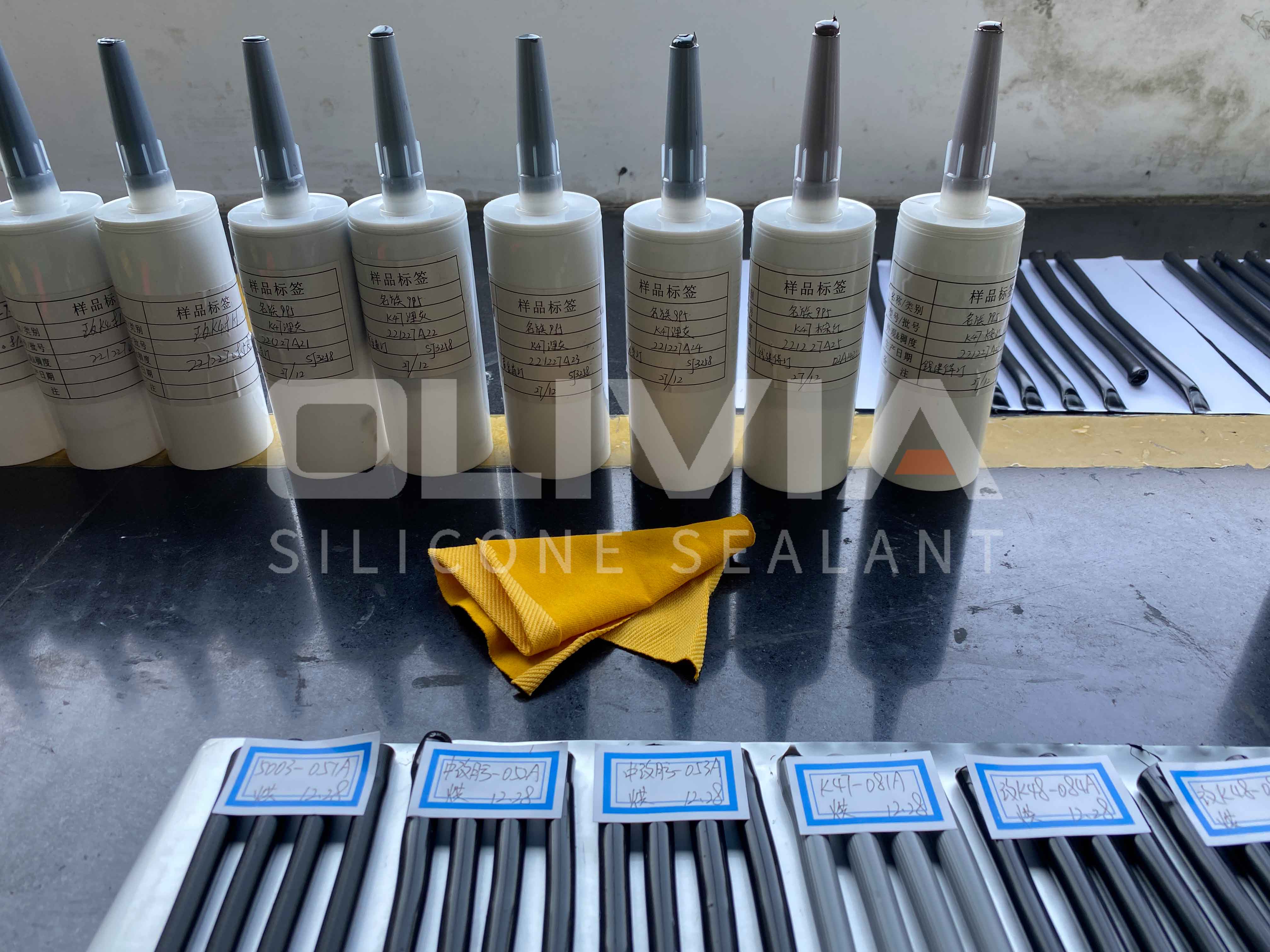
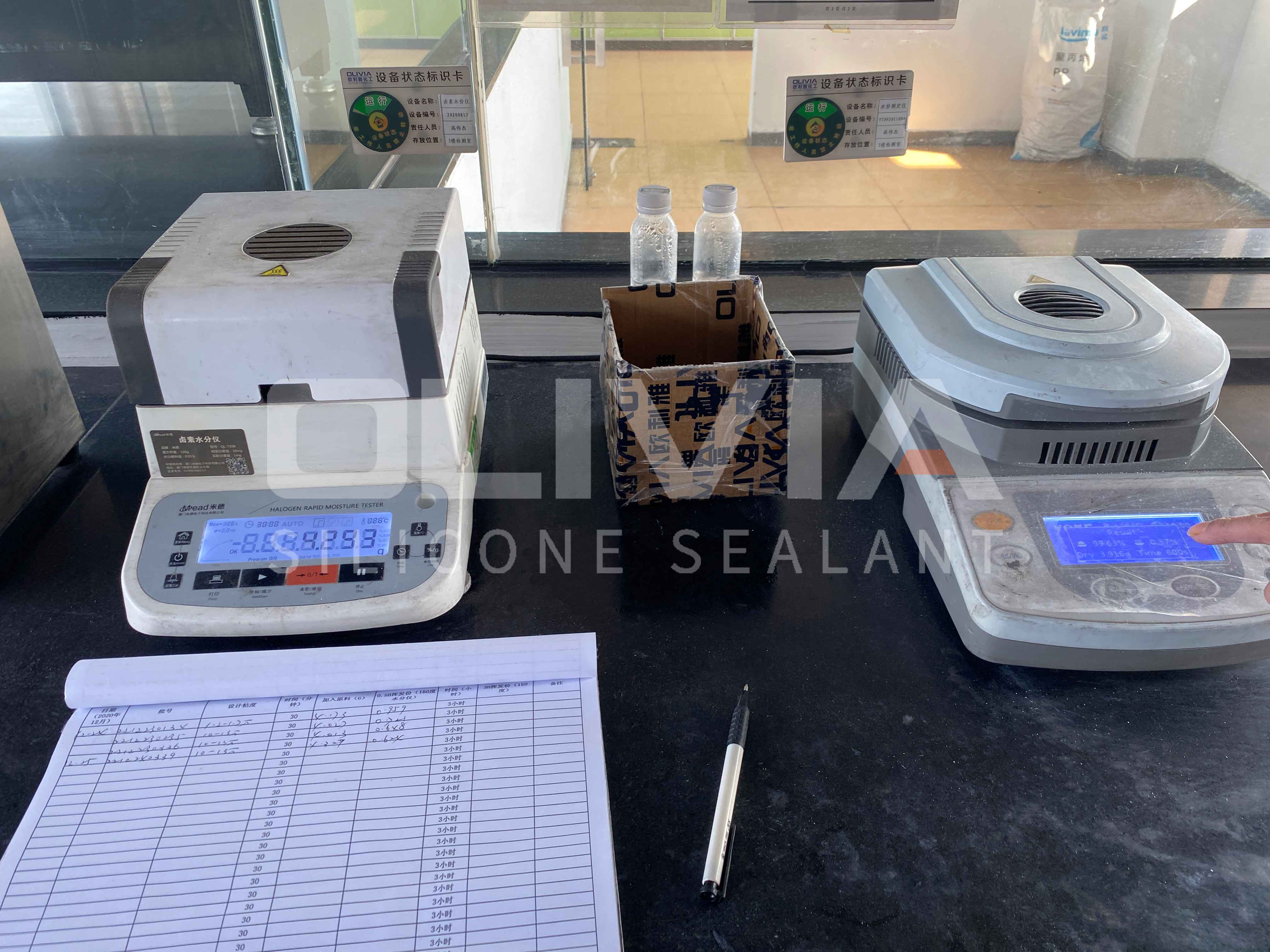
کچھ حتمی تجاویز
ایک حصے کے سلیکون دستیاب اعلیٰ ترین معیار کے سیلنٹ ہیں۔ ان کی حدود ہیں اور اگر مخصوص ضروریات کا مطالبہ کیا جائے تو انہیں خاص طور پر تیار کیا جا سکتا ہے۔
یہ یقینی بنانا کلیدی ہے کہ تمام خام مال جتنا ممکن ہو خشک ہو، فارمولیشن مستحکم ہو اور پیداوار کے عمل میں ہوا کو ہٹا دیا جائے۔
تیار کرنا اور جانچنا بنیادی طور پر کسی بھی ایک حصے کے سیلنٹ کے لیے ایک ہی عمل ہے، قطع نظر اس کی قسم - صرف اس بات کو یقینی بنائیں کہ آپ نے پیداوار کی مقدار بنانا شروع کرنے سے پہلے ہر ممکنہ پراپرٹی کو چیک کر لیا ہے اور یہ کہ آپ کو درخواست کی ضروریات کا واضح اندازہ ہے۔
درخواست کی ضروریات پر منحصر ہے، صحیح علاج کیمسٹری کا انتخاب کیا جا سکتا ہے۔ مثال کے طور پر، اگر سلیکون کا انتخاب کیا جاتا ہے اور بدبو، سنکنرن اور چپکنے کو اہم نہیں سمجھا جاتا ہے لیکن کم لاگت کی ضرورت ہے، تو ایسیٹوکسی ہی راستہ ہے۔ تاہم، اگر دھات کے پرزے جو کہ corroded ہو سکتے ہیں شامل ہیں یا ایک منفرد چمکدار رنگ میں پلاسٹک سے خصوصی چپکنے کی ضرورت ہے تو آپ کو ایک آکسائم کی ضرورت ہے۔
[1] ڈیل فلاکیٹ۔ سلیکون مرکبات: سائلینز اور سلیکونز [M]۔ Gelest Inc: 433-439
* اولیویا سلیکون سیلنٹ سے تصویر
پوسٹ ٹائم: مارچ 31-2024